Distribution
- AULS
-
Automated Unattended Loading Solutions
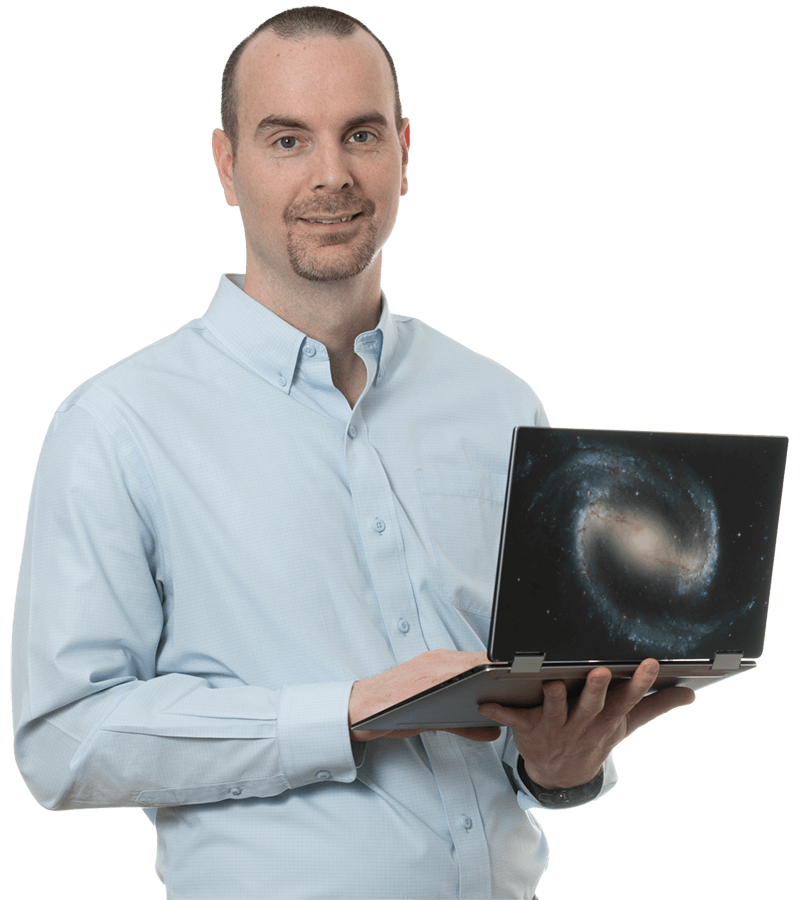
Customers have told me having a cement plant without SSLS or Plant Portal is like having a McDonalds® without a drive-thru.
Craig Leavitt
VP · Distribution
Complete Control
The Ultimate in Plant Automation Delivers Maximum Capacity
Self-Service Loading System (SSLS)
“Wouldn’t it be great if we had a system that was so foolproof that the drivers could load themselves?”
Out of this basic idea PSCL’s Self-Service Loading System (SSLS) was born. Drivers load up earlier and later in unattended mode allowing them to avoid heavy traffic patterns. In areas with multiple options for purchasing cement, transport companies go out of their way to load product at locations with SSLS installed.
Training the driver takes less than 10 minutes with our Follow the Green™ software. Every time they use it you’re saving time and money, and combine it with other technologies to increase safety, security and ROI.
Safety and security are paramount to PSCL. We have made risk reduction an integral part of SSLS, and designed it to fit within a larger product suite that enhances the safety, security, effectiveness and efficiency of your site. By combining the SSLS with our other products, you have the advantages of an integrated, easy-to-understand system designed specifically for the cement industry:
- Limit access to authorized users who have a valid order in the system
- Manage authorized users with our Self-Service Administration application, giving site operations the power to control access
- Together, Order and Loading Management automatically replicate the transaction to your ERP system and to the SSLS kiosk
- Monitor the site with Integrated Site Video Management for a real-time view of all loading activity
- Manage site access, enable automated and unattended loading, and direct traffic flow using Plant Portal kiosks
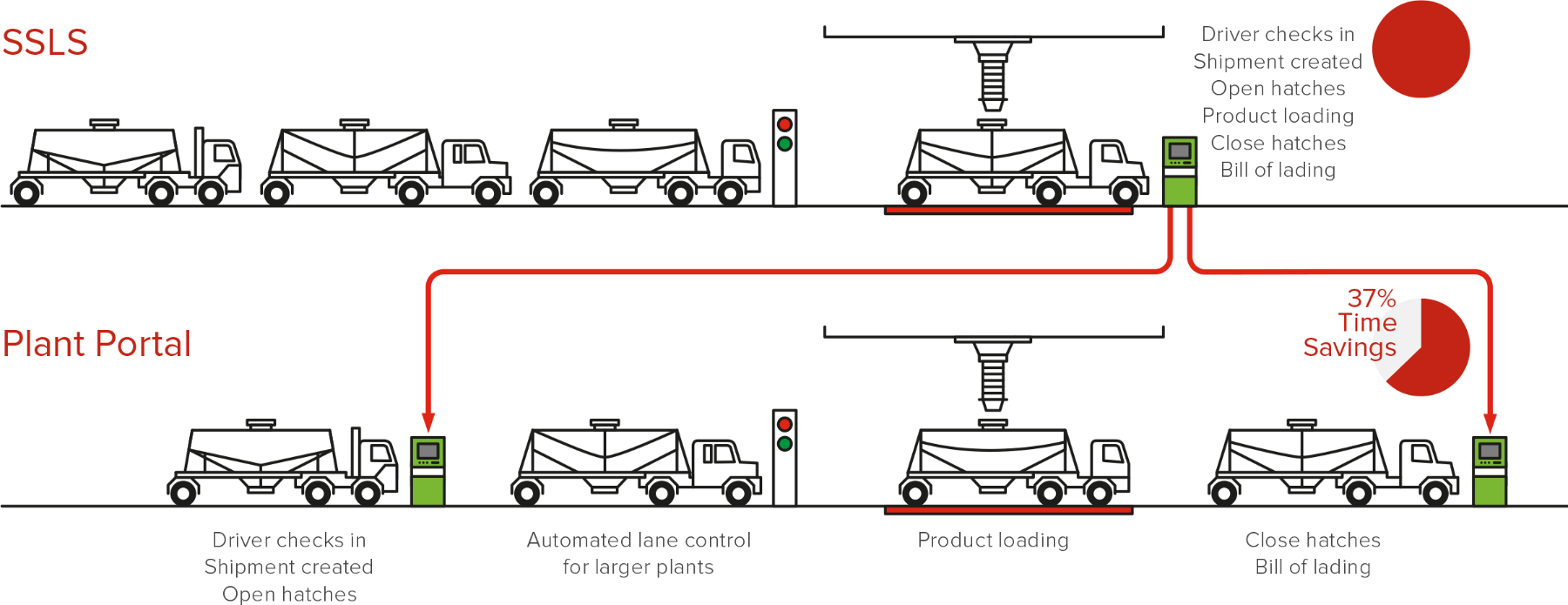
Self-Service Loading reduces labour and interaction time by having the driver fulfill their own order through our kiosk. With Plant Portal, the primary benefit is reducing time on scale to only product loading. Order generation, bill of lading and other administrative tasks are done before or after loading. On average, you move a third more product in the same time.
Plant Portal
PSCL’s Plant Portal controls access to your site, directs traffic, keeps drivers on task, minimizes time on scale and has drivers print their own BOLs. The perfect compliment to an efficiently-run and cost-effective terminal, freeing your staff from mountains of paperwork.
Plant Portal is implemented with kiosks placed at the site entrance and alley exit locations for signing in and out, accepting the shipment, and printing out their BOL. It is the best way to reduce scale time – by as much as 37 per cent – eliminating the bottleneck in your delivery system. In addition, Plant Portal allows complex loading scenarios like simultaneous loading for dual-trailer trucks.
Cement customers prefer Plant Portal. It is the No. 1 cement terminal management solution in North America. Your customers expect the convenience, accuracy and efficiency that Plant Portal provides. They will choose it time and again to keep their costs low and minimize their valuable time loading.
Shipping
Plant Portal is a flexible, adaptable solution configured to meet your logistical priorities.
- Optimize plant logistics by reducing time spent on tasks such as check-in and check-out
- Reduce time on scale and improve loading efficiency
- Minimize driver wait times with automated alley selection, based on current queuing and average load times
- Reduction of plant manpower requirements for shipping activities providing significant cost savings

Driver Management
SSLS and Plant Portal link to video cameras to take pictures of the driver and their rig, or use RFID cards and driver signatures to verify the driver’s identity and associated sales order. As an added bonus, the system uses a stored tare weight to detect retained product to avoid cross contamination.
- Manage site-specific indoctrinations, be notified when they expire
- Manage sales order allocations easily
- Check credit limits from your financial system before loading
ERP System Integration
SSLS and Plant Portal synchronize your contacts (drivers, companies), sales orders, inventories, credit statuses and transactions with your ERP system. Our tool kit enables us to adapt to your ERP implementation quickly.
- SAP
- Oracle
- JD Edwards
- All others that support data exchange
Raw Material Receiving
- Eliminate manual process of tracking receipt of goods
- Provide validation of received quantities
- Automated integration of receipt transactions into ERP, thereby reducing costs and improving accuracy
- Manage unloading activities and prevent driver errors
- Streamline accounting functions such as payables creation and vendor payments
Combine it with our other technologies to automate more of the loading process:
- Notify the loader that the driver has arrived, and signed into the site with Loading Management
- Sync the sales orders to SSLS and Plant Portal kiosks with Order Management
- Monitor the trucks movements on site with Integrated Site Video Management
- Track and report total time onsite, loading times and accuracy with Loading Management
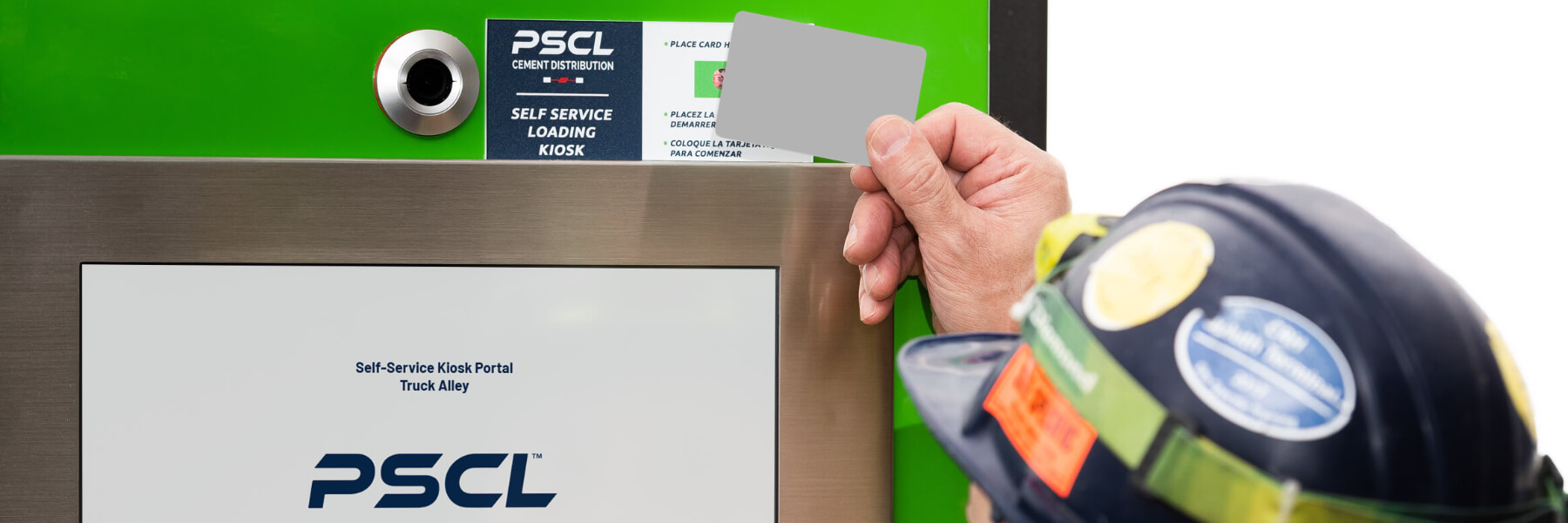
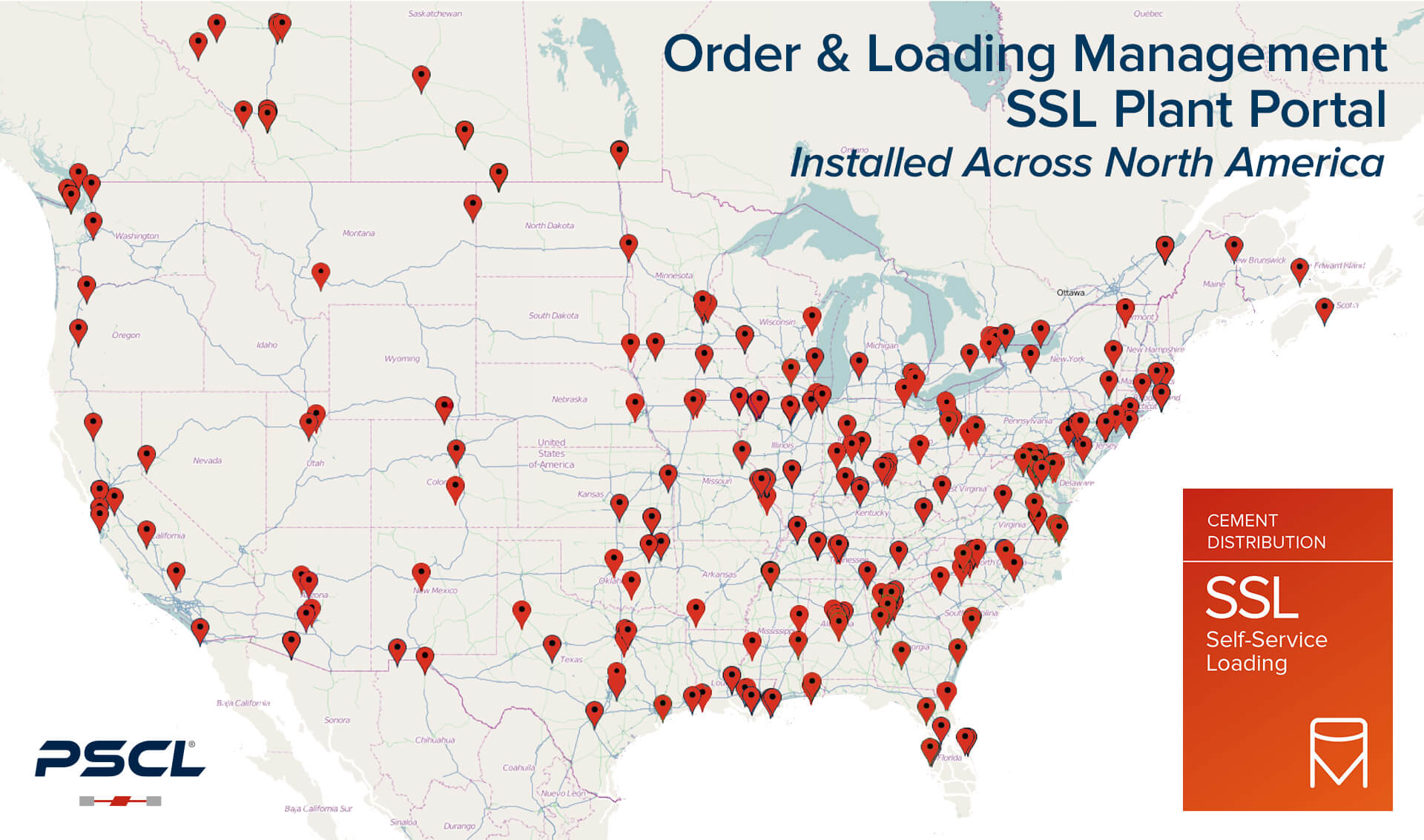